随着 5G 时代的兴起,由于材料特性所限,第 1代(Si 等)、第 2 代(GaAs 等)半导体材料器件性能无法满足输出功率等的要求,以 GaN、SiC 为代表的第 3 代半导体的研究又被推到了新的高度。以通讯及国防领域有着重要应用的 GaN 射频器件为例,其市场从 2018 年的 6.45 亿美元将增长至 2024 年约 20亿美元。但随着功率密度的提升,随之而来的热效应剧烈增加,已经成为制约 GaN 基半导体器件发展最重要的瓶颈,经过近年来的发展,热流密度已至数百 W/cm2 ,而若要达到器件理论极限,热流密度将再度提高 1 个数量级,器件热点处热流密度几近太阳表面热流密度,这也对散热材料提出了新的需求:器件热量密度不均匀,需要更高的导热性能进行均温;热量密度提升,需要更优的主动散热方式带走热量。传统散热材料以金属及合金、陶瓷材料等为主,金属材料有着较高的热导率,但在封装过程中存在导电的风险;而陶瓷材料绝缘性好,强度高,但热导率较差,随着装备小型化、轻量化的要求,以热导率/密度(λ/ρ)的比值成为评判材料散热性能的新参数。以 Kovar、Invar、氧化铝为代表的材料低于 10 W·cm 3 /(m·K·g),一般作为密封及结构材料,热性能较差;传统散热材料其 λ/ρ 所处区间一般为10~100 W·cm 3 /(m·K·g),如金属铜、银、部分合金及SiC 等,但随着半导体器件的跨代发展,对散热材料的需求也急剧提升,λ/ρ 达到铜 10 倍以上的金刚石材料逐渐崭露头角,有着轻质高强、超高热导率、绝缘性好等其他材料难以企及的优势,受到了学术界和产业界的广泛关注。目前,人造金刚石主要存在高温高压法(HPHT法)及化学气相沉积法(CVD 法) 2 种制备方法,HPHT 法主要用于单晶块体颗粒金刚石的制备,由于制备过程采用金属催化剂且含较多氮杂质,传统HPHT 法制备金刚石多成黄色小颗粒状,随着产量及制造水平的提升,部分无色宝石级 HPHT 金刚石已进入市场,但颗粒尺寸仍较小,无法满足各形态的散热需求。而 CVD 法中的微波等离子体化学气相沉积法(MPCVD 法)制备的金刚石具有生长工艺稳定,纯度高,可大面积制备易成膜,热导率高等优点,因此被广泛用作雷达组件等超高热流密度条件下的散热材料。然而我国虽然人造金刚石总产量达全球 95%以上,但主要为 HPHT 金刚石,由于“Wassenaar 协定”的限制,“发展和生产电子器件用金刚石衬底或薄膜技术”被以美国为首的多国禁运。因此,发展自主知识产权的 MPCVD 设备是金刚石散热产业化的关键。基于此,本文主要以 MPCVD 设备为基础,通过金刚石不同晶态延伸出不同的散热应用场景,介绍了近年来一些典型的金刚石散热应用最新研究进展,并阐述和概括各项技术路线的技术问题和发展方向。
MPCVD 是目前公认制备高品质金刚石的方法,最早于 1983 年由 Kamo 等[8]提出,其基本原理是将磁控管产生的2.45 GHz微波经矩形波导管导入石英管中,H2、CH4 混合气体在强电场作用下发生解离,分解为原子氢、甲基等 20 余中不同碳氢基团,根据 Harris 和 Goodwin 提出的生长模型,仅原子氢及甲基是直接参与金刚石生长,扩散至基体表面形核及生长,从而实现金刚石薄膜的沉积,其所使用的功率和气压较低(300~700 W、1~8 kPa),因此金刚石生长速率一般不足 3 μm/h,远不足以达到产业化批量生产及应用的要求,主要存在以下问题:1) 微波谐振腔设计优化不足,导致腔体内部电场强度低,电离困难,等离子体密度低,生长速率偏慢;2) 局域电场强度小导致等离子体电离区域小,又因微波场强集中区域为受限于 2.45 GHz 微波半波长61.2 mm,难以扩大沉积面积;3) 样品冷却困难,提高功率密度过程中热量积聚于样品,若要保持生长适宜温度,需及时将热量导出,样品连接及冷却尤为重要。
为进一步提高金刚石品质和生长速率,又发展出了多种形式的 MPCVD 金刚石生长系统,根据沉积腔体的结构可分为:石英钟罩式、圆柱金属谐振腔式、环形天线(CAP)式、椭球谐振腔式以及一些其他类似的结构形式,其中,圆柱金属谐振腔式 MPCVD 沉积腔体为带水冷的不锈钢夹层,与石英钟罩式 MPCVD 系统相比,允许更高的微波功率输入,但 2 者均存在等离子体刻蚀石英,导致金刚石膜中存在 Si 杂质污染的问题。CAP 式谐振腔的微波输入窗口设置在样品台下方,远离等离子体放电区域,减少了等离子体对石英窗的刻蚀,提高了系统高功率下运行的稳定性。椭球形谐振腔利用椭球 2 个焦点对微波电场的聚集效应,使得等离子体位置不依赖于微波输入功率和气体压力,能够在沉积台上方稳定激发,该系统实现了 6 kW、14 kPa、直径 5.0~7.5 cm的沉积面积,但石英钟罩的存在同样会导致等离子体刻蚀石英污染金刚石。经过几十年的发展,目前几种 MPCVD 金刚石生长系统已经能够在0.5~8.5 kW、0.5~40.0 kPa 条件下运行,功率密度和沉积面积也逐步提升,部分研究组研究设备及性能如表 1 所示。
表 1MPCVD 设备性能及研究单位
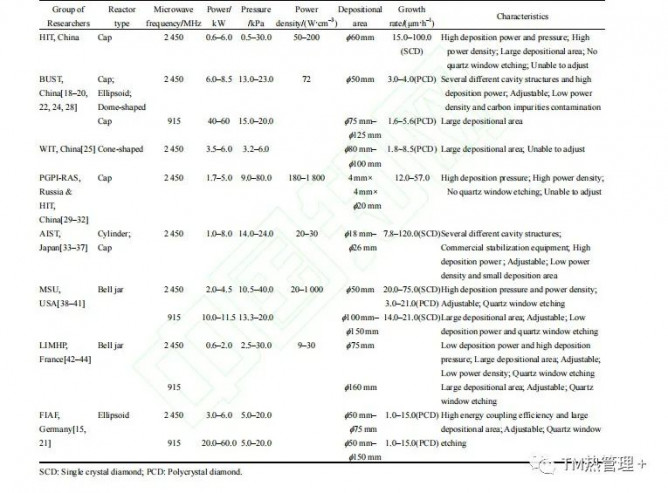
从 MPCVD 金刚石生长系统的发展历程可以看出,该系统设计的核心目标是实现大尺寸均匀高密度等离子体稳定激发,同时应保证等离子体贴近衬底基座且无次生等离子体对石英窗口的刻蚀。由于微波传输过程中所有金属边界都会对电磁场谐振产生较大影响,因此该系统的设计是一个十分复杂的问题,其关键在于最佳边界条件的获得。通过对不同边界下的微波电磁场进行计算机仿真模拟,能够在一定程度上预测系统性能,实现微波谐振腔的快速优化,再结合 Füner 等提出的唯象模型以及Yamada 等提出的流体模型可以对系统等离子体密度、温度等特性进行预测。国内北京科技大学、武汉工程大学、西安交通大学等单位均开展了 MPCVD 金刚石化学气相沉积系统的研制工作,并进行了金刚石生长制备,近年来优化了能量密度及均匀性,但部分设备仍存在石英刻蚀、控温困难等限制高品质金刚石沉积的关键问题。哈尔滨工业大学朱嘉琦教授团队采用多目标协同设计的微波谐振腔优化方法,综合考虑等离子体均匀性与高密度,对微波传输与等离子体激发进行系统设计优化,设计微波传输–散热一体化结构解决控温难题,实现电子密度>2×1017 m –3 的等离子体稳定激发的金刚石生长系统,在保证等离子体高能量密度的均匀分布的前提下扩大沉积尺寸,解决了晶圆级单晶金刚石生长的基础设备问题。但是用于金刚石生长的设备研发并未停止,在解决上述问题后,针对微波频率的稳定性、微波能量的单一性问题,仍会是今后研究需要攻克的方向。随着GaN 器件的发展,第 3 代半导体固态微波源即将取代磁控管,成为大功率高稳定微波源模块化、小型化的必然选择。此外,多束能量耦合激发等离子体如射频、激光等能量的加入也将为 MPCVD 设备开启新篇章。
单晶金刚石是金刚石材料体系中热导率最高的,这与其晶体结构密切相关,碳原子由高强度 sp 3共价键相连,是典型的共价键晶体,主要通过晶格振动即声子导热,而晶体热导率由热容、声子平均自由程、声子速度决定。金刚石晶格非谐振动弱,声子平均自由程长;Debye 温度高,声子速度快,因此金刚石热导率极高。而在实际应用中热阻也是与热导率同样重要的参数,代表着热量传递过程中受到的阻碍,是热导的倒数。绝对热阻是单位时间内当有单位热量通过物体时,物体两端的温度差,而由于 2 种材料连接的界面晶格中断,热载流子无法全部导致产生温差形成的热阻即为界面热阻。哈尔滨工业大学近年来与俄罗斯科学院合作,制备单晶金刚石热导率达 2400 W/m·K,并对 mosaic拼接单晶金刚石的界面热阻进行了分析(图 2)。单晶金刚石用作散热主要有 2 种方式,一种是直接用作替代外延衬底,原位生长材料制备器件,通过器件有源区与金刚石紧密接触利用金刚石超高的热导率将热量均匀分布到衬底中;另一种是在单晶金刚石结构中加入微通道结构,利用流体将内部热量带出,达到降温的目的。2 种方法各有优劣,近些年发展较快。
图 2 哈尔滨工业大学制备金刚石热导率随温度变化
单晶金刚石表面外延器件是随着分子束外延技术(MBE)和金属氧化物化学气相沉积(MOCVD)的发展而兴起。2009 年,Dussaigne 等利用 MBE 方法在单晶金刚石的(111)面异质外延了单晶 GaN,表面粗糙度可达 1.3 nm,光致发光谱测试光学性能良好,开辟了外延 GaN 器件的新道路。次年,Dussaigne 等又在单晶金刚石(111)面通过 AlN 过渡层制备了GaN 粗糙度降低到 0.6 nm,在其表面又制备了高迁移率的Al0.28Ga0.72N/GaN 二维电子气材料,室温电子迁移率可达 750 cm 2 /(V·s),为金刚石衬底器件制备奠定基础。同年,Alomari 等也制备了迁移率类似的材料体系,以此制作了 0.2 μm 栅长器件,电流密度可达 0.73 A/mm。Hirama 等在 Ib 型金刚石表面同样制作了 3 μm 栅长的金刚石基高电子迁移率晶体管(HEMTs),电流密度 0.22 A/mm,截止频率3 GHz,最高振荡频率 7 GHz,此外,由于金刚石优异的导热性能,器件热阻首次降低到 4.1 K·mm/W,相比传统 SiC 衬底的 7.9 K·mm/W 大大降低,2 W 功率下器件温度降低了 10 ℃。次年,作者制备栅长0.4 μm HEMT 器件电流密度提升至 0.77 A/mm,首次实现金刚石基 HEMTs 功率输出,1 GHz 时功率密度2.13 W/mm,采用热导率更高的 IIa 型金刚石,将热阻进一步降低至 1.5 K·mm/W。
图 3 金刚石(111)面生长 AlGaN/GaN HEMT 示意图
Schuster 等将 GaN 纳米线生长于单晶金刚石(111)表面,在不使用催化剂及缓冲层的条件下,实现自组装生长过程,并展现出与当时最先进的Si 基 GaN 纳米线相近的性能,为金刚石与 n 型氮化物的结合应用奠定基础。Hetzl 等已形成自组装及区域选择性生长 2 种完善的金刚石表面 GaN纳米线制备方法,在此基础上,完成了 p 型金刚石和 n 型 GaN 纳米线异质二极管的制备,具有良好的整流特性和电致发光特性。2021 年该课题组又完成异质外延单晶金刚石(001)晶面上 GaN 纳米线的制备,推动了大尺寸产业化金刚石基高频高功率器件的应用发展。但是,单晶金刚石基器件仍面临着外延层晶格常数及热膨胀系数差距大,单晶衬底难以大尺寸批量制备,以及成本过高等难题,待异质外延单晶金刚石质量及产能突破后发展潜力巨大。
图 4 金刚石及 SiC 基 GaN HEMTs 器件性能对比测试
Tuckerman 等提出了微流道热沉的设计理念,可以通过周期性改善流动混合以及通过产生二次流来增加湍流率来提高传热系数。高热流密度器件采用金刚石衬底,提升面内均热效果,结合微流道,将热量更快导出,必然将带来更高的散热效率,然而由于金刚石难以加工,一直以来金刚石微流道散热研究进展较为缓慢。随着飞秒激光的发展,Shinoda 等利用 800 nm 波长的飞秒激光在金刚石表面加工出40 nm宽,500 nm深,长0.3mm的微槽,并且该结构仍然保持原本金刚石成分。2013年,Su 等采用1 026 nm 波长的 Yb:YAG 激光在金刚石表面制备了约 410 nm 深的微流道,证明了单晶金刚石表面微流道制备的可行性,相比于传统聚焦离子束(FIB)和反应离子刻蚀(RIE)方法,激光加工金刚石可以更快更方便地加工三维结构。Jedrkiewicz 等基于脉冲 Bessel 光束激光加工单晶金刚石,调节激光能量和写入速度,控制了微槽的表面粗糙度等参数,对微通道内部微流体控制提供了极大帮助。
中国研究主要类似于 Müller 等采用的金属掩膜过渡生长的方法,在金刚石表面利用金属制备掩膜版,金刚石生长过程中会产生横向外延过程(ELO)覆盖金属掩膜,从而形成金刚石槽道。Fu 等采用金属钨和 ELO 过程制备微流道并通水实验,微流道截面尺寸 10 μm×1 μm,但由于 ELO 生长表面闭合过程,微流道截面呈 T 字形,影响其流动特性。次年,结合电感耦合等离子体(ICP)方法,增加了金刚石微流道深度,可达 20 μm 以上,为金刚石微通道的应用更进一步。崔健磊教授团队,采用纳秒、飞秒激光对多晶金刚石的加工进行了深入研究,系统研究了激光能量、扫描速率、扫描次数、焦点位置等参量及其优化工艺参数对金刚石微槽尺寸的影响规律,对激光烧蚀阈值进行了预测及实验,加工出侧壁锥度 3°内的高质量金刚石微流道。为进一步提升散热性能,将其激光加工方式推广至单晶金刚石,与哈尔滨工业大学及中国电科 38 所合作,开发应用于雷达功率组件的单晶金刚石微流道散散热器,热流密度可达1.38 kW/cm2,远远优于传统多晶金刚石微流道散热达到的 267 W/cm2及 473.9~1 000.4W/cm2。这对中国雷达组件、高能数据中心等超高热流密度应用场景发展有着极大推进作用。

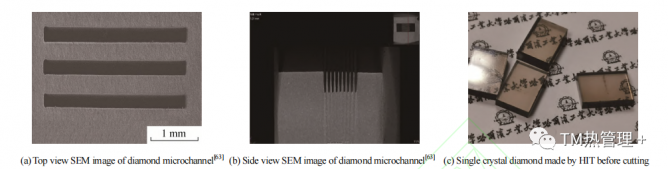
目前,将金刚石作为功率器件的热沉或衬底目前已报道了多种技术形式,其中主要有:基于衬底转移技术的金刚石键合,基于金刚石钝化层的低温沉积以及金刚石上的器件外延生长。由于键合技术作为一种更为灵活的并行工艺,因此对于大功率半导体器件散热更具有吸引力。但早期的键合实验一般在 800 ℃高温进行,并且大尺寸高导热单晶金刚石尚未制备,且需要引入低热导率的界面键合材料,从而导致器件性能优势无法充分发挥。现阶段,多晶金刚石与 Si、GaN、Ga2O3 等的室温键合已经通过表面活化键合(SAB)技术实现,从而大大降低了器件与金刚石之间的热膨胀失配。最先开展 GaN/金刚石低温键合方法的是英国航空航天公司(BAESystems),其技术路线首先在 SiC 基 GaN 外延层制备 HEMT 器件,然后将 GaN 基 HEMT 晶片键合在临时载体晶片上,去除 SiC 衬底和部分 GaN 形核层和过渡层,并将其表面和金刚石衬底加工到纳米级粗糙度;随后在 GaN 和金刚石衬底分别沉积键合介质(键合介质可能为 SiN、BN、AlN 等),在低于 150 ℃的温度键合,最后去除临时载体晶片最终获得金刚石衬底 GaN HEMT 器件。团队早期制备的直径 25 mm 金刚石衬底 GaN 结构键合成功率达到70%,随后采用该技术路线将金刚石衬底 GaN 晶片推广到 75~100 mm。除 BAE Systems 外,Mu 等采用表面活化键合法在室温采用 27 nm 厚 Si 键合层制备出金刚石衬底 GaN 晶片,实现了界面层的无缝界面。富士通公司利用极薄 Ti 膜作为保护层结合SAB 技术成果将 GaN 的 SiC 衬底和金刚石相结合,避免离子束轰击带来的界面损伤,获得了较低的界面热阻(67 m2 ·K/GW)。中国方面,北京科技大学已经获得 100 mm 热导率大于 1 500 W/(m·K)金刚石膜,在加工抛光后基本满足低温键合对尺寸、热导率及表面光洁度及面形度等方面的基本要求。在此基础上,南京电子器件研究所(NEDI)与北京科技大学合作,将直径 75 mm 的 GaN HEMTs 外延层转移到多晶金刚石衬底上。但该技术的挑战在于实现大尺寸接合面的极低粗糙度和均匀抛光以及超高真空的要求。此外,原子扩散键合(ADB)是另一种很有前景的低温键合技术,其中在每个光滑干净的表面上溅射金属薄膜,然后在压力下在接触界面上实现原子扩散和金属键合。特别是 Au 具有较高的自扩散系数(300 K 时为 3.3×10–29 m2 /s),且表面无氧化层形成,满足大气环境和常温键合加工的要求。目前,基于键合理论目前常用键合方法还有:共晶键合、瞬态液相(TLP)键合、阳极键合、亲水键合、混合键合等。
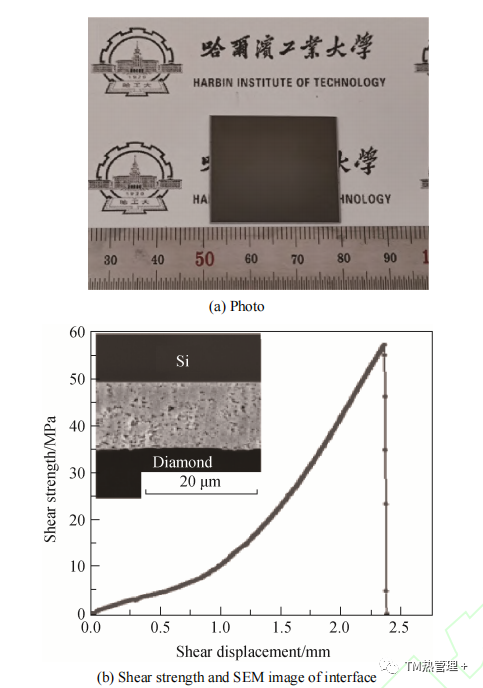
然而,在实际操作中,功率器件通常会通过器件模块中的焊锡键合直接安装到金刚石散热器上。焊锡键合广泛用于器件集成,因为它不需要非常低的材料表面粗糙度,并且还可以在相对较低的温度下实现键合。但是,用于焊料键合的 AgSn [33 W/(m·K)]和AuSn [57 W/(m·K)]的热导率比金刚石低2个数量级,厚度为焊料层通常大于 100 μm,会引入高界面热阻,因此这种方法通常被认为不适合与金刚石集成的功率器件。由于纳米/微米银粒子具有烧结温度低(< 300 ℃)、烧结后熔点高(960 ℃)、导热系数高[>200 W/(m·K)]等诸多潜在优势。因此,它在电子封装领域得到了广泛的应用,例如芯片互连以及芯片与金属或陶瓷基板的连接。然而,对于金刚石,大多数金属或合金难以有效润湿其表面,且浆料在烧结过程中有机物挥发和界面中的黏合剂分子难以烧尽,多数情况下烧结银粘贴仅适用于 10mm×10mm 或更小尺寸的接口连接。基于该技术结合酸洗–等离子体双步法对金刚石表面活化处理,增强界面连接,有效降低连接热阻,在 220℃烧结实现了大面积金刚石散热器和 Si 芯片(27 mm×28 mm)的低宏观界面热阻(TIR)和高强度结合。Si–金刚石键合系统的 TIR 可小于 500m2 ·K/GW,同时剪切强度大于 50MPa。它表明在各种电子组件中的互连以及在激光设备中产生尺寸稳健的接合或高功率设备的热管理方面具有广阔的应用前景。
2.3 纳米金刚石材料
纳米金刚石膜材料用作散热一般为高热流密度器件钝化层,传统器件一般采用氮化硅为钝化层,防止外界环境波动对功能层的影响,但热导率极低,若采用金刚石材料替换传统钝化层,可在器件表面进行均热,为器件增加一条导热通路,提升器件表面均温性能。但氢等离子体对氮化镓具有反应刻蚀作用,导致器件直接沉积金刚石的方法需要低温条件并且需要耐氢设计。在耐氢保护层表面,金刚石需要均匀高密度形核,同时需要高定向排列,以提升金刚石钝化层整体导热能力。由于氮化镓器件表面不平整,大面积钝化层沉积过程中由于非平整表面带来的应力和不连续性会影响到整个器件的可靠性,这些都为金刚石钝化层制备带来较大的困难。Seelmann-Eggebert 等对 GaN 场效应晶体管(FETs)表面制备纳米金刚石钝化层展开探索,从保护层、形核、沉积工艺等多方面入手,完成了在GaN-FETs 表面 440 ℃条件下 0.7 μm 及 480 ℃ 2 μm纳米金刚石沉积,但是器件性能提升并不明显。这是由于在低温条件下,氢等离子体刻蚀作用较差且二次形核过程显著,晶界处 sp 2 过多,金刚石质量较差导致热导率降低,但仍是首次将金刚石应用在GaN 器件表面进行散热,开创了先河。Alomari 等经过 54 h 在 GaN 表面制备出 6.2 μm 的金刚石薄膜,利用 SiO2 及 Si 过渡层,提升了金刚石的生长温度及金刚石质量,首次进行了器件性能测试。美国海军实验室(NRL)对纳米金刚石增强 GaN 基 HEMT 器件大信号功率特性的影响进行了研究,在 4 GHz 时,输出功率密度为 5.8 W/mm,增益 10 dB,功率附加效率达 32.6%,表明了纳米金刚石对于 GaN 器件的热管理有较大应用潜力。NRL 又采用氧等离子体刻蚀金刚石膜层进行器件加工,未对器件性能产生损伤,对纳米金刚石钝化层与传统 SiN 钝化层器件进行对比,得出金刚石结构要远优于传统结构的结论。哈尔滨工业大学与中国电科 55 所合作,研制纳米金刚石钝化 GaN 器件,探究了不同过渡层电位的异种电位形核方法,提升了初期形核密度,调整纳米金刚石生长过程参数,采用红外无接触循环退火方法大幅降低金刚石与氮化镓等异质材料的界面应力,在 600 ℃制备晶粒尺寸可控纳米金刚石钝化层,实现高导热金刚石层对器件表面的全覆盖,GaN HEMTs 器件电流密度提升 20%。此种方法基底尺寸灵活性高,可制备晶圆级大尺寸晶片,原有产线工艺调整较小,在产业化方向有着较大优势,是目前较为有潜力的方法。但仍存在纳米金刚石热导率相比单晶热导率较差,散热效果有限的问题,仍有进一步探索的空间。表 2 总结了本文所述部分金刚石器件散热方法优劣及性能参数。
表 2金刚石增强散热方法及性能比较
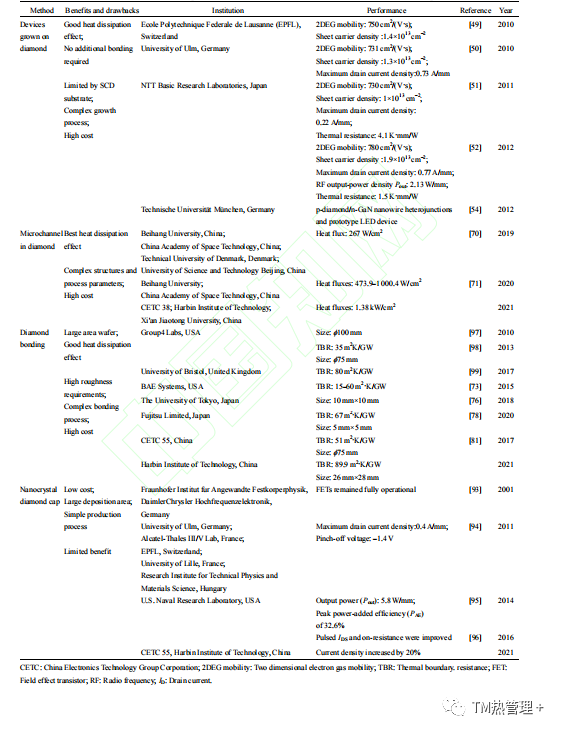
从金刚石的生长设备出发,对已报道的设备形式及制备金刚石散热应用进行整理及总结。伴随着半导体器件和摩尔定律的发展及小型化轻量化的需求,热流密度正在逐步递增,引领着散热材料和散热方案的改变。对于散热材料,轻质高热导率成为发展的目标,金刚石成为最优选择之一。高温高压金刚石产业方面我国已占据绝对优势,而各企业也在积极寻求产业转型,MPCVD 方法由于其工艺可控,制备金刚石品质高、杂质少的优点引起了广泛的重视及研究,MPCVD 金刚石逐步走出实验室开始产业化进程,但是现今产业化 MPCVD 设备大多仍采用圆柱金属谐振腔式面向宝石级钻石应用而设计,虽然生长速率较快,但难以扩大生长面积,应用中存在诸多问题,难以打破“瓦森纳协定”对我国“金刚石衬底及薄膜”方面的限制。尺寸的扩大才能带来成本的降低,而目前大尺寸金刚石生长装备的研制进展缓慢,大多采用 2.45 GHz、915 MHz 磁控管微波源作为微波发生装置,存在稳定性和功率受限的问题,同时,需要构建新型多目标微波谐振腔优化方法,针对大尺寸、高均匀及高等离子体密度进行设备优化,保证大尺寸下的高速高品质生长。此外,微波源的能量种类复合也有望解决现有问题。第 3 代半导体 GaN 固态微波源在输出效率、功率密度、体积等方面有着巨大优势,且功率合成设计简便,采用其替代磁控管是近期大功率 MPCVD 设备的发展方向。而引入多种能量复合,如激光增强、射频增强微波等离子体研究较少,或将成为新的研究热点。设备的发展也为着材料服务,随着 MPCVD设备瓶颈的逐个解决,超级导热金刚石材料将极大地推动学术发展乃至工业进步。而针对半导体需求,金刚石生长的“大、纯、快”是目前遇到的难点问题,大尺寸单晶晶圆的制备,高纯电子级金刚石的可控生长等难点的解决,将为金刚石产业发展带来新篇章。
高热流密度器件散热方案经过多年的发展,逐步从远端自然冷却过渡到近结主动液冷乃至相变散热,热流密度也提升至 kW/cm2 级别,超高导热金刚石材料的加入虽然对散热效果有了提升,但是实际应用中仍存在诸多难题亟待解决。具体地,单晶金刚石作为衬底材料仍存在着尺寸受限、价格高昂的缺点,这与生长设备息息相关,也是产业研究的重点;单晶外延 GaN 材料仍无法大面积实现,电性能也有所降低,GaN 沉积技术日趋完善,实现大面积 GaN 高质量外延,提高电学特性是其发展方向;大尺寸多晶金刚石的键合及纳米金刚石钝化在器件中的应用较为相似,存在经济性好、制备流程简单、可大面积制备的优点,但是其性能受界面热阻的影响较大,高界面热阻限制了高热导率带来的增益,如何有效测试界面热阻,优化连接过程,改善异质连接状态,降低界面热阻至关重要,也是现在研究的热点。因此,解决上述材料问题,发展配套装备技术,将为金刚石高效散热提供更广阔的应用前景,也有望推进以 GaN 为代表的第三代半导体器件性能,更进一步接近理论极限。
来源:硅酸盐学报
作者:赵继文 1,郝晓斌 1,赵柯臣 1,李一村 1,张森 1,刘康 1,代兵 1,郭怀新 2,韩杰才 1,朱嘉琦 1,3
1. 哈尔滨工业大学 特种环境复合材料技术国家级重点实验室
2. 南京电子器件研究所 微波毫米波单片集成和模块电路重点实验室
3. 哈尔滨工业大学 微系统与微结构制造教育部重点实验室
(来源:DT半导体)