这种柔软的太阳能电池,可以装在车窗或者房屋的玻璃上。在炎热的夏天,既能吸收红外光,降低内部空间温度,同时又可以发电。不过这种柔性电子材料,很难用传统的蒸镀制备方法实现。
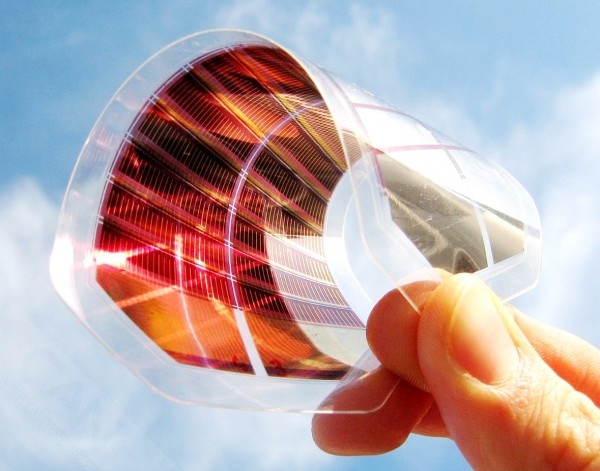
以硅为例,它的熔点是1414℃。生产时,就要先升温超过熔点,获得单晶硅,再把单晶硅切分成小块,组装成电子元件。这是一种自上而下的生产方式,而且由于需要高温环境,非常耗能。常见的3D打印,也离不开高温环境,通常要加热到几百度。
如果换一种生产方式呢?像用墨水打印文字一样,同样用液体作为基底,把电子材料的分子打印成需要的结构。这就是溶液打印法,是“自下而上”的打印思路。要做到这一点,就需要对分子进行精细地控制。
目前美国伊利诺伊大学助理教授刁莹和她领导的小组研究的方向就是:通过调控分子组装过程,利用溶液法来打印电子材料。
流体控制技术:让电子流动更高效
溶液打印不是一个新的技术,“我们到新的地方在于可以控制到纳米甚至分子层面的结构。”对比普通的3D打印,只能控制到微米级别。“中国唐代已经有印刷术了。虽然不太像我们现在做的事情,但是基本的道理是一样的。”刁莹说。印刷报纸的时候,需要把墨水打印到想要的地方;打印电子材料,还要考虑到被打印材料里面的结构是怎样的。
分子层面的溶液打印,就是以有机溶液为载体,将分子打印成所需要的结构。这种方式,只需要20多度的室温条件。因为是以溶液作为打印基底,利用对溶剂的流体控制,也很容易打印柔性材料。
电子材料对于结构的控制要求非常高。进入微观层面,分子的结构、形态,即使微小的变化,都会对最终的材料性质产生影响,有时甚至是数量级的改变。如何精细地控制分子的结构?这就需要利用分子的自组装特性。分子会依据其特性,自发地从无序变为有序,通过一些方式进行引导,就可以让分子按需排列。
刁莹实验室最近的一个发现,是将原来卷曲的高分子结构拉平,从而实现更好的光电性能。共轭聚合物富含电子,单键和双键交替,这是让电能快速传播的关键,因此共轭聚合物具有很大的电气光学应用潜力。但是也存在问题,这些聚合物的形态通常是扭曲,严重阻碍电荷传输。
施加巨大的压力,或改变共轭聚合物的分子结构,虽然可让其变得扁平,但这两种方式都需要密集的劳动力,很难进行大规模量产。刁莹团队发现,在分子打印过程中,受到溶液流动体的引导,共轭聚合物的分子可以在一个特殊阶段变成平面形状,并在溶液沉淀后继续保持这一形态。发现了这个机制后,刁莹团队希望能够进一步研究它的普遍性,让流体控制技术在溶液打印中更广泛使用。
创新打印方式:动态模板
2018年,刁莹经历了一次艰辛的突破,她尝试了新的研究概念——动态模板。她和团队的伙伴们做了很长时间,最终证明了“动态模板”这一方法在分子溶液打印中的可行性。此前,在分子组装中只有类似于“静态模板”的技术。2014年的诺贝尔物理学奖颁给了蓝光LED材料的三位研究者,其中一项突破就是采用了这种技术。制造蓝光的LED材料缺乏单晶体底衬,研究者采用蓝宝石作为底衬,设计出高序列的结构,从而控制蓝光LED的材料有序生长。
“动态模板”的概念则受到了自然界生物矿物质合成的启发。“我们观察自然,被生物系统的方式所启发。”刁莹介绍到。但是不仅仅如此,这其实是一次逆向思维的过程。
刁莹在博士期间的研究方向本是药物结晶,但她却被生物矿物质的形成机制所吸引。自然界的珍珠就是通过动态模板来实现离子组装的。
高分子的动态模板本身非常无序,但是却可以引导矿物质离子形成有序的结构。原因在于模板和聚集的矿物离子之间会彼此协同。离子会在模板附近形成凝聚层,动态模板也会调整自己,来适应离子所需要的结构。
在溶液打印中,刁莹想寻找到更有效方法来组装高分子,沿用已有的底衬设计思路非常困难。“高分子结构本身非常复杂,在生物矿物质合成的过程中,是高分子来组装离子,在我们的系统中,需要组装高分子,我就想,能不能用离子来组装高分子。”
研究最终证明,通过动态模板技术,能够打印出高度取向、高度结晶的聚合物薄膜。这项控制分子组装的技术有广泛使用的潜力。
制造未来的材料
刁莹所带领的研究小组,目标是理解基本分子组装过程,来控制打印材料的特性,最终为医疗设备、能源等领域提供节能高效的材料制造。
2016年,她在研究柔性太阳能电池方面取得突破。通过控制纳米层面的结构,加快电荷的分离速率,从而提高光电转化效率。2020年开始,她的团队继续之前的研究,从更微观的分子层面来控制结构,进一步提高光电转化效率。同时,她们也在研究如何控制分子的自组装过程,让打印出来的太阳能电池更加稳定。溶液打印速度快,又适合打印大面积的材料。她想通过自己的努力,让这一打印方式有更广泛的应用。
当初,她做出选择,从药物结晶领域转到有机电子材料,就是希望能离可应用的技术近一些,想看到自己的研究对现实真正产生影响。目前,电子材料的主流制作方法还是蒸镀。“蒸镀的方式其实是很贵的,像我们买的智能手表,显示屏是最贵的原件。如果能用溶液打印的方法,可以大幅度降低成本。”